Casting - Kirloskar Ferrous
Casting
Koppal Plant | Solapur Plant | ||
Features | Line 1 | Line 2 | Line 3 |
Capacities/Annum | 60000 MT | Phase I - 48000 MT Phase II - 24000 MT (Cum 72000 MT) |
42000 MT |
Moulding | High pressure mould line air impact(HPML) | High pressure mould line squeeze type (HPML) | High pressure mould line squeeze type(HPML) |
Moulding Line Establishment year | 1994 | 2014 | 2008 |
Mould box size(mm) | 1250x900x400/400 | 1300x1000x400/400 | 1000x800x350/350 |
Facility | Fully Finish Machining | Semi-Finish Machining |
We have modern 3D Core Printing facility. KFIL produces prototype castings of different varieties using 3D printed cores/molds and pouring in the regular HPML. These castings are made in shortest record time to support our customers for immediate Proto-requirements.
KFIL has been accredited with following certificates:
1. ISO 140001 Certificate
2. IATF 16949 Certificate
3. ISO 45001 : 2018 (OH&S) Certificate
Our facility at Koppal is located close to the iron ore deposits of the Hospet-Sandur-Bellary belt, which allows us to backward integrate to the Blast Furnace to our Foundry. Similarly, the Solapur plant has a casting manufacturing facility with forward integration to a semi-finish machining facility. Both plants have highly productive equipment and skilled manpower along with tactical supply-chain-logistics. Our facilities can produce a range of products that includes Grey Iron castings from 30 kg to 300 kg single piece weightand Pig Iron of Foundry grade, SG grade and Basic Grade. Preserving the planet for the future is always on top of our minds. Towards that end, we effectively utilize the waste gas from the Mini Blast Furnace by powering three Power plants aggregating to 11.5 MW.
In 2014, we commissioned a new foundry with High-Pressure Mould Line, Robotic Core Centre and advanced processing capabilities, as well as an in-house casting fettling and finishing shop with advanced and highly productive equipment.
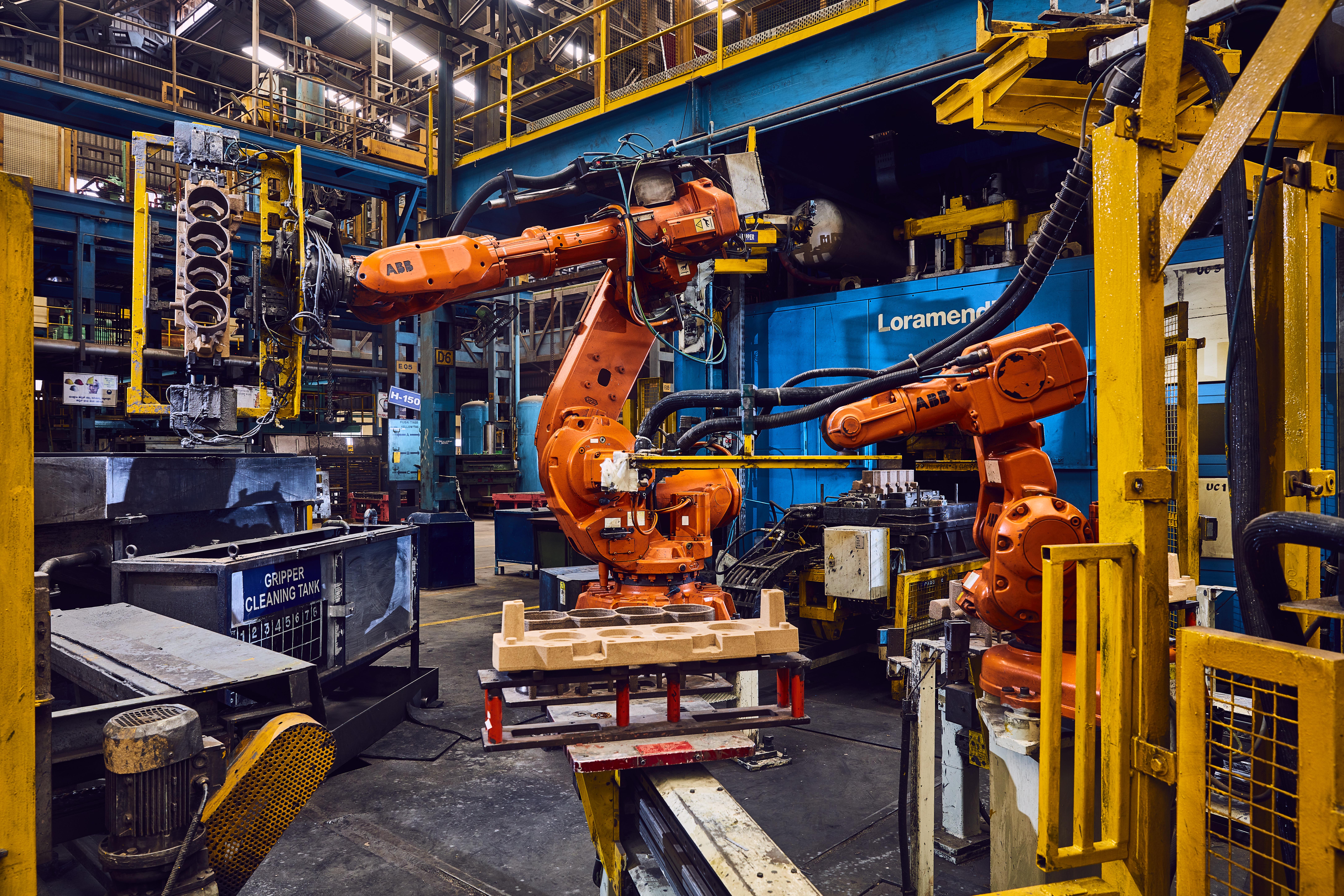
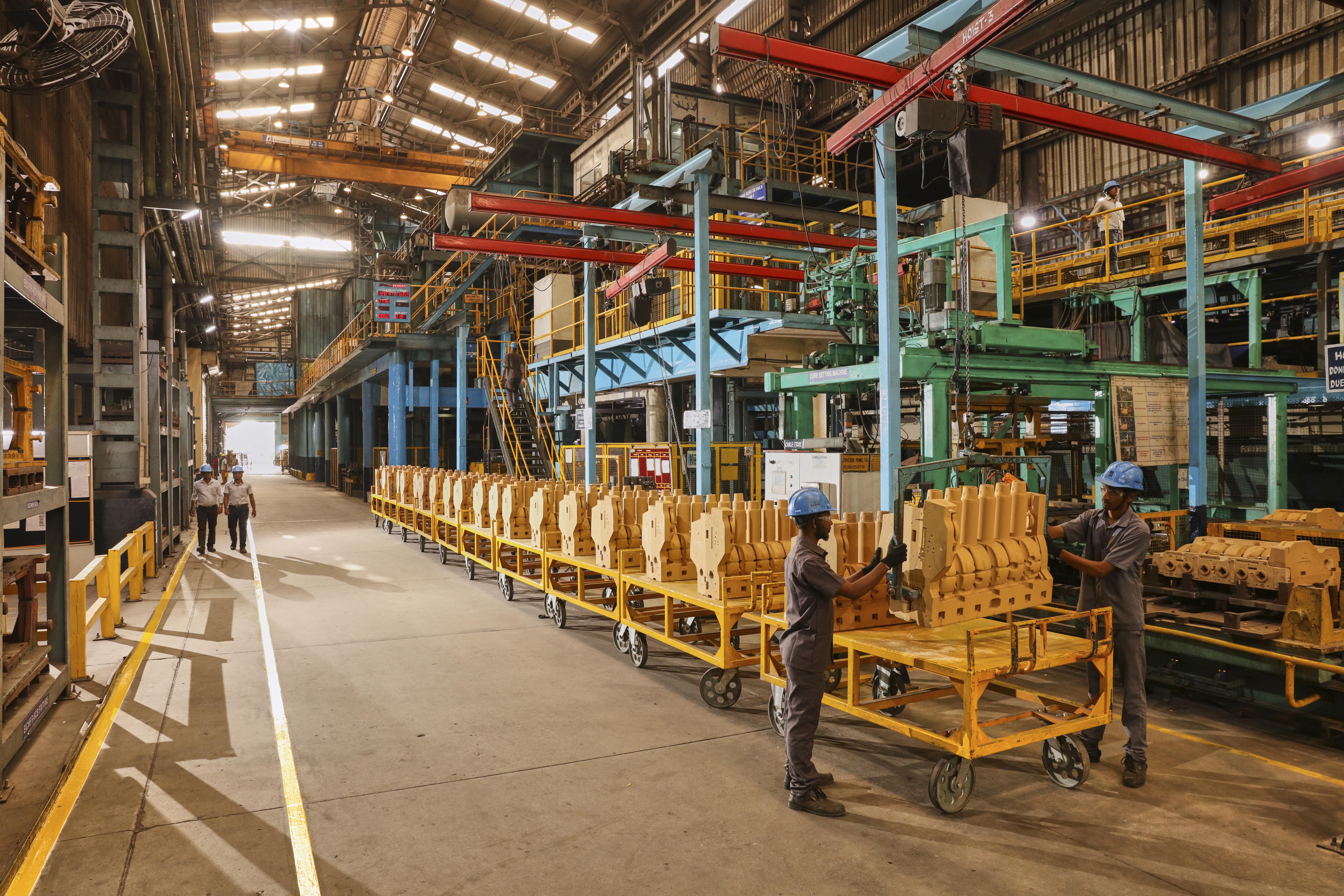